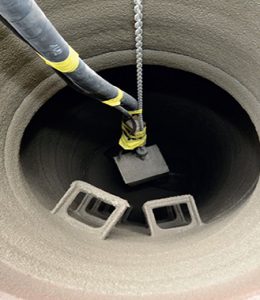
Manholes are defined as a confined space and can suffer from both neglect over the years and also serious chemical attack from hydrogen sulphide gas within both water and petrochemical industries. Other market sectors where manholes can suffer from degradation is the dairy industry due to the build-up of lactic acids, Alcohol and soft drinks manufacture due to the high sugar and citric contents and washing down and cleaning of plant and equipment within the manufacturing industries where acid and alkaline solutions are used in the cleaning process and then processed through effluent drainage systems.