Grit blasting / Abrasive Cleaning
Service
Services
Contact For Services
Total Specialist Maintenance Ltd (TSM) is a leading specialist contractor Driven to exceed expectation!
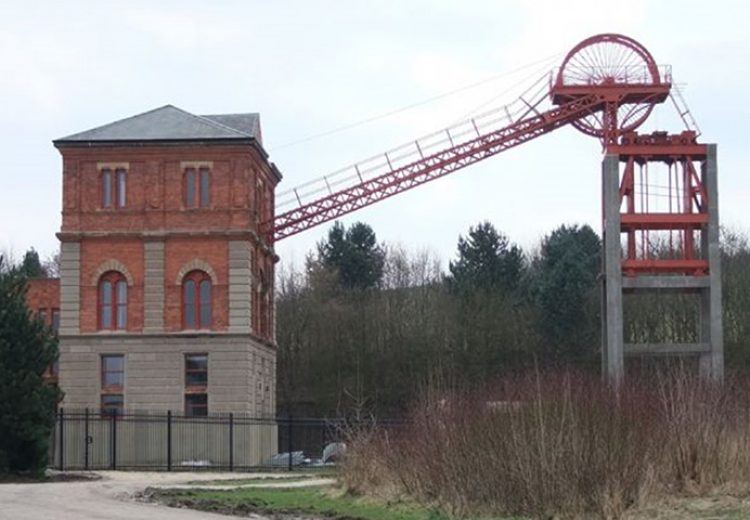
Grit blasting / Abrasive Cleaning
Total specialist maintenance provide specialist Grit blasting services to bridges, subways, manholes and chambers, Steel structures, concrete and masonry structures, car parks on a national basis and for various market sectors
Total specialist maintenance carries out all forms of grit blasting and surface preparation which include Dry grit blasting, Wet blasting, Sponge blasting and vacuum track blasting.
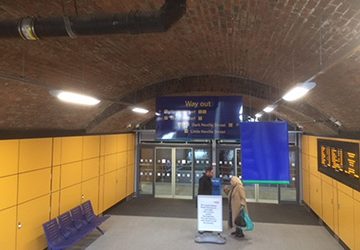
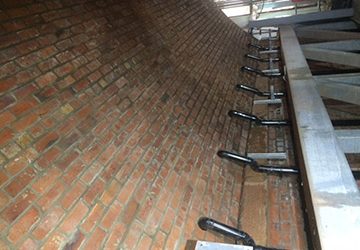
Requirement for blasting and surface preparation
Grit blasting is often simply used to improve the aesthetic appearance of structure/buildings, however, grit blasting is predominately used to remove existing coatings and paints and to provide surface preparation for the application of protective coatings to concrete, masonry and steel substrates.
Wet blasting/Sponge blasting is used to remove poisonous coating such as lead based paints, these techniques are used to ensure that the containment of air bourn contaminates are eliminated and can be safely removed from site.
Vacuum track blasting is used to prepare floor slabs in preparation for the application of protective floor coating systems.
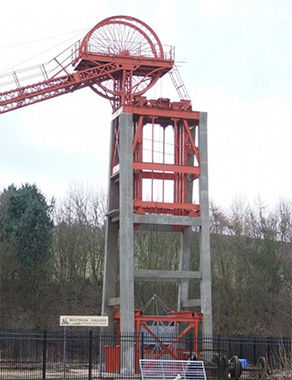
Services
Traditional Grit blasting
Vacuum Blasting
Wet blasting
The removal of poisonous coatings
Remedial wall ties
The removal of poisonous coatings
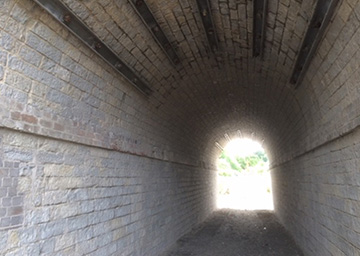
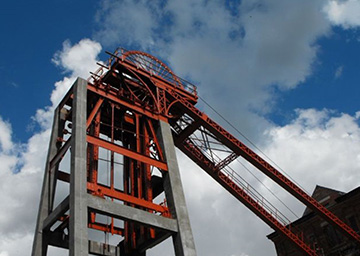
Sectors
- Aviation Industry, Bridges and Tunnels, Buildings, Construction Industry, Education, Food And Drink Industry, Health Care, Heritage And Listed, Highways, Hotel and Leisure, Local Authorities, Marine Structural Refurbishment, Ministry of Defence, Multi-storey Car Park, Nuclear, Petrochemical Industry, Pharmaceutical Industry, Rail, Social Housing, Water Industry
Benefits
Directly Employed Workforce
Highly Skilled and Experienced Operatives
Certified Training
Accreditations
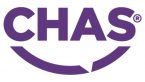
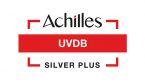
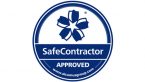
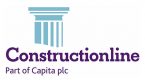
Frequently
Ask Questions
Technical Questions About
Grit blasting and abrasive cleaning
Frequently asked questions about Total Specialist Maintenance grit blasting and abrasive cleaning , for domestic, highways, Water industry, rail and infrastructure sectors and technical queries regarding grit basting and abrasive cleaning
For any additional information that is not listed please contact our technical team
Grit blasting is a technique that creating surface textures by the impact of hard particles. The particles hit a metal surface/masonry surface at high velocity, causing localized plastic deformation. The resulting texture is influenced by the shape, size, hardness, and velocity of the shot particles using high-speed particles.
There are different types of abrasive/ grit blasting which include grit, stone grit silicon dioxide, soda, steel, bristle, glass beads, and much more. All these different grit blasting methods are used to achieve a smooth/textured surface by making use of a specific type of grit sometimes to remove coatings or in preparation for the application of coatings.
Abrasive Blasting is the correct term – Sandblasting is often used mistakenly. Both Sandblasting and Abrasive Blasting are used in today’s industrial vernacular. The terms mean generally the same thing: the removal of the top layer of a substrate, coating, contaminant, or corrosion through airborne abrasives.
Shot blasting is typically used on metal parts to clean the parts. Beads are shot through a machine to remove impurities trying to restore the part to its original condition. – Grit blasting is a process that remove surface contaminants or coatings and is used to smooth/textured surface by making use of a specific type of grit, sometimes to remove coatings, or in preparation for the application of coatings.
Natural Abrasives – Calcite, Diamond, Iron oxide, Sand, Sandstone, and powdered feldspar. Synthetic Abrasives – Borazon, ceramic, aluminum oxide, dry ice, glass powder, steel abrasive, silicon carbide, and slags.
Traditional grit blasting – Typically this involves open blasting or encapsulated blasting where required with no special requirements other than removal of coatings, preparation of substrate and removal of contaminants.
Wet blasting – is an abrasive media and water. It eliminates the poisonous particles from becoming airborne during the blasting process and blasts the surface at the same time. This all aids in the removal of poisonous materials such as lead. This also aids with cleaning process as the media and contaminants remains wet throughout the process. Once the wet blasting has been undertaken there may be a requirement to flash blast the substate to remove any flash rusting.
Trac blasting -Blastrac closed circuit media shot blasting machines throw a large amount of steel abrasive media by centrifugal force at the surface. After the steel abrasive hits the surface, the shot blaster recycles the media. Dust and contaminants are removed by an air wash separator and are removed to a dedicated Blastrac dust collector. This makes the process almost dust-free in operation.
Shot blasting with steel shot is the most environmentally friendly abrasive blasting method there is, because there is no use of chemical products and no waste of valuable drinking water. The video below shows the shot blasting process perfectly.
To clean and prepare surfaces | such as steel, concrete and asphalt.
To remove top layers | like paint and epoxy.
To remove markings & rubber | from highways, runways, industrial floors and more.
To improve skid resistance | on surfaces such as sidewalks, bike paths, roads and runways.
To generate optical and aesthetics effects | on surfaces like roads, highways and runways.