Bridge Deck Waterproofing
Service
Services
Contact For Services
Total Specialist Maintenance Ltd (TSM) is a leading specialist contractor Driven to exceed expectation!
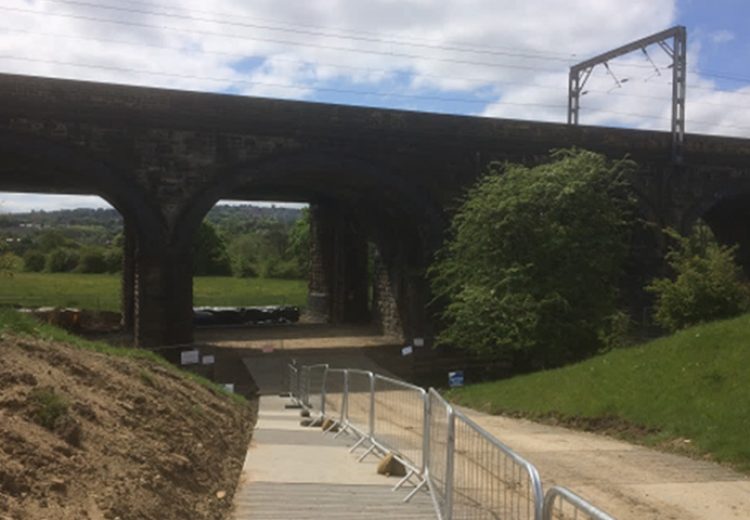
Bridge Deck Waterproofing
Total specialist maintenance provide Leak sealing resin injection waterproofing services to bridges, tunnels, subways, on a national basis and for various market sectors such as the rail and highways
We work closely with MC Building Chemicals to supply and install the GL95 elastomer injection bridge deck waterproofing system. This system is applied to brick, stone and steel bridges and tunnels throughout the UK.
The GL95 elastomer gel injection structural waterproofing system has been installed to numerous Network Rail and highway structures as a successful solution. It is considered as being the most economical bridge deck waterproofing service within the rail industry, especially where the removal of the permanent way and expensive line possessions are undesired as all works are carried from the underside of the structure.
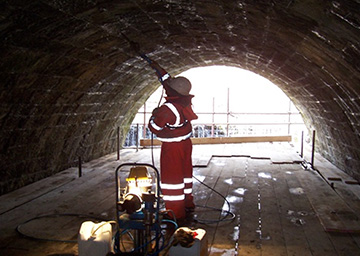
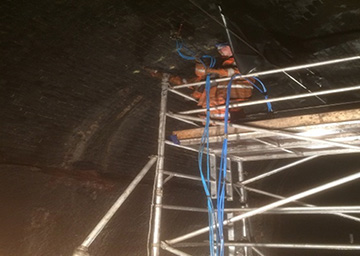
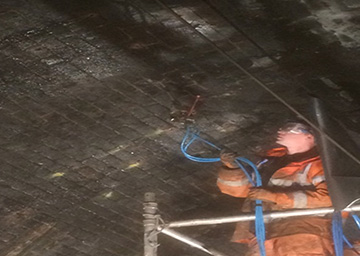
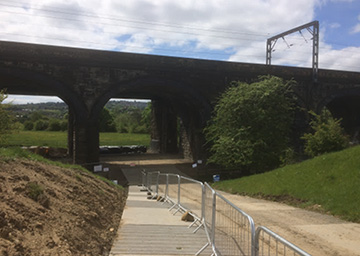
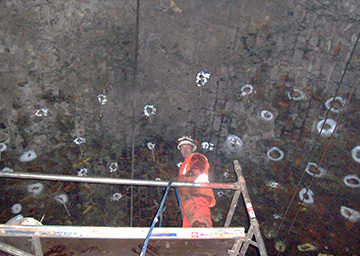
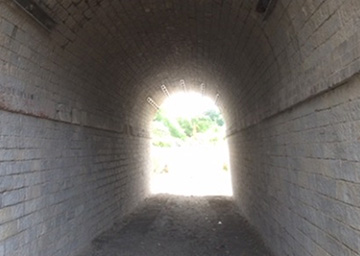
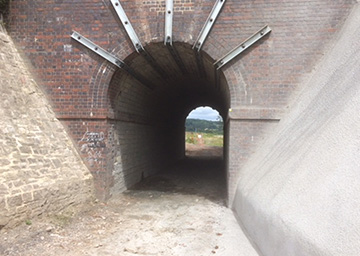
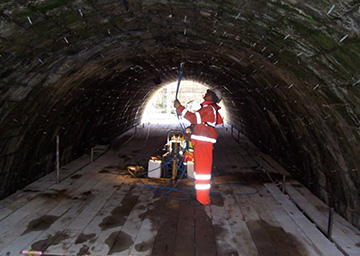
All of our works are carried out without any disruption to the local rail or road network. As a full bridge deck waterproofing company our service will protect against water infiltration, chloride attack and chemicals such as diesel/petrol fuels.
MC Building Chemicals leak sealing hydrostructural elastomer / acrylic gel technology has been embraced by the UK and European Rail and Highways sector, becoming the accepted alternative to traditional waterproofing, offering solutions and eliminating disruption and excessive costs.
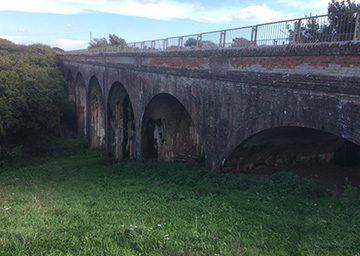
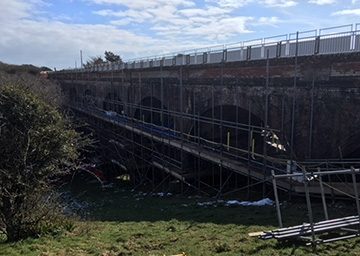
Problems that require bridge deck waterproofing
Corrosion from years of precipitation
Previous waterproofing systems failing
Carbonation of the reinforced steel
Spalling brick work and degradation of stone work
Problems that require leak sealing resin injection waterproofing
Water bearing defects that require Leak sealing resin injection waterproofing include, expansion joints, movement joints, water bearing cracks, honey combed concrete, structures where existing waterproofing has failed, leaking joints in pre cast concrete sections, pipe penetrations, service penetrations, Steel/cast iron trough decking and plate decking defects.
Services
Elastomer gel injection systems
Foaming Polyurethane injection systems
Polyurethane injection systems
Leak sealing injection of steel trough deck structures
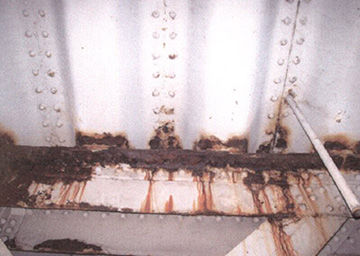
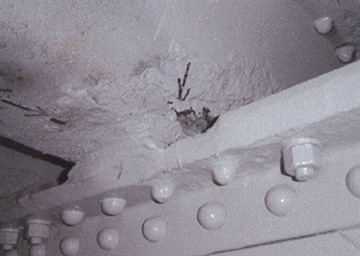
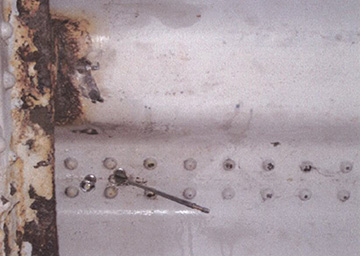
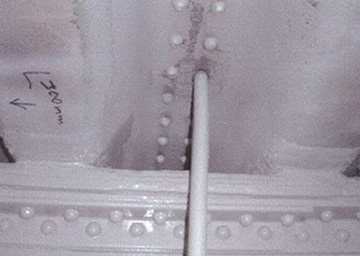
Leak sealing injection of cast iron deck structures
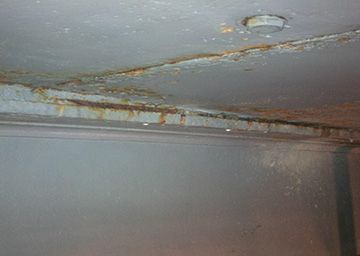
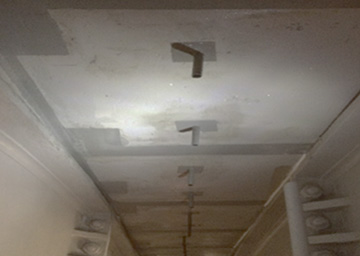
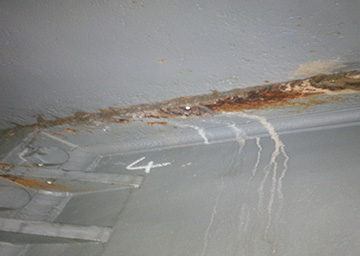
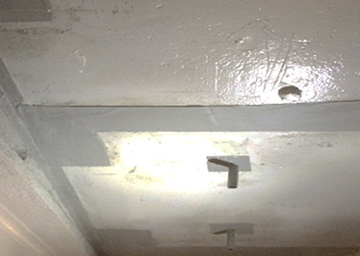
Benefits
Directly Employed Workforce
Highly Skilled and Experienced Operatives
Certified Training
All operatives are PTS trained
Accreditations
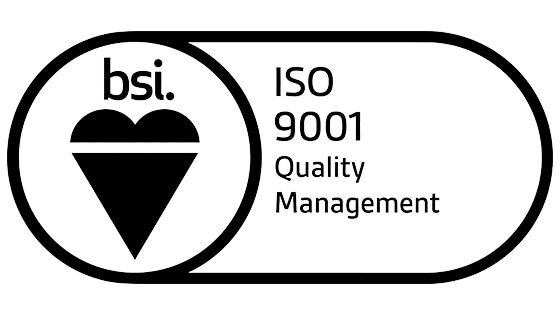
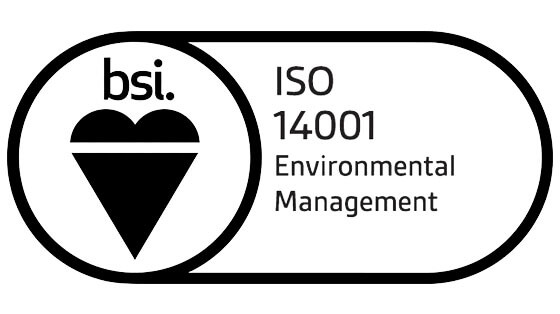
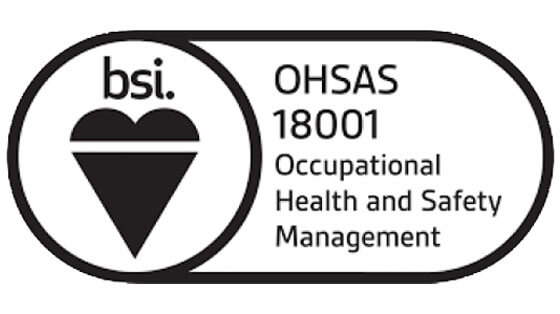
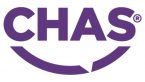
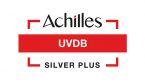
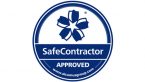
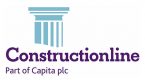
Frequently
Ask Questions
Technical Questions About
Bridge deck waterproofing
Frequently asked questions about Total Specialist Maintenance bridge deck waterproofing, for rail, highways, local authorities, housing developers and infrastructure sectors and technical queries regarding bridge deck waterproofing
For any additional information that is not listed please contact our technical team
To increase the durability of reinforced concrete bridges, all concrete movement and construction joints, plus the bridge decks have to be waterproofed to prevent serious damage to the concrete, or to the embedded steel reinforcement.
Stops water from penetrating through bridge cracks, which leads to freeze-thaw damage to the bridge deck and underside of the bridge. Furthermore, moisture and oxygen will oxidize and corrode steel parts of the bridge, which cause further cracks and spalls that worsen corrosion. Leaking masonry bridges can also degrade from water penetration causing spalling bricks, cracks, voids and defective pointing causing structural issues.
Bridges are busy sites that have open exposure to a host of contaminants, not to mention multiple trades working together simultaneously. It’s best to choose a bridge deck waterproofing system that can be repaired on-the-spot if the membrane does get damaged. This helps keep the bridge construction on track.
For our injection waterproofing system we carry out flood testing of the structure post the initial injection installation to identify any leakage within the bridge structures which is “tightened up” by carrying further resin injection
For our spray applied systems we carry out adhesion testing followed by spark testing which identifies if there is any defects within the coating.
Ask manufacturers both for references from long-term bridge projects as well as accelerated age testing data to see how the membranes have performed over the ensuing decades since they were applied.
Choosing a bridge waterproofing membrane that can be sprayed on fast and cures quickly is the first step. However, the real application time often comes down to what weather and temperature restrictions there are for applying the waterproofing system. Many liquid waterproofing systems are highly sensitive to moisture.
Unfortunately, this means we have to wait around for the right weather conditions before they can apply the waterproofing. This puts added pressure on bridge owners, who may face complaints from the public the longer construction or lane closures go on. Choosing a waterproofing system that is less moisture sensitive helps avoid these delays. This can also be highly beneficial for clients, who are often rewarded based on completion time.
Our resin injection system is not sensitive to weather and moisture and actually benefits from water and moisture being present. Our injection system is usually installed from the underside of the bridge which eliminates the requirements for railway tracks to be lifted and road surfaces to be removed which enables the client to keep services running, however where roads and railway tracks run underneath the bridge our system can be carried out during railway possession, road closures and lane closures.
As we are an approved installer of all the major bridge deck waterproofing systems we have all of the necessary quality control procedures in place to ensure the systems are installed correctly and carry out a full Q/A procedure which includes checking substrate preparation, correct mixing procedures, sample testing, application coverage, curing times, pull off tests, spark tests and flood testing.