Concrete Repair
Service
Services
Contact For Services
Total Specialist Maintenance Ltd (TSM) is a leading specialist contractor Driven to exceed expectation!
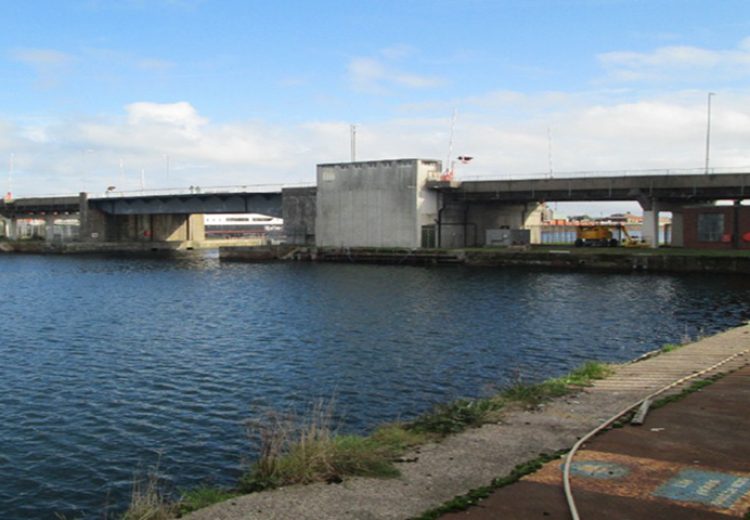
Concrete Repair
The main causes of concrete structure degradation
Carbonation
The process of chemical reactions taking place where areas are exposed to the elements.
Chloride
Usually from sea water causing an autocatalytic process to take place, not on the concrete but on the reinforcing steel that is being used.
Distilled Water
In the form of steam, distilled water can wash out calcium content in concrete, leaving it in a brittle condition
Concrete repair services
Total specialist maintenance are an approved installer of all of the major concrete repair material manufacturers product range, we work hand in hand with the material manufacturers to develop the most appropriate and cost effect repair specification to ensure that the client is provided with the best solution to enhance the life the structure.
Total specialist maintenance offer an free initial advisory service, that can be followed up with a concrete testing survey to identify the causes of the damage and defects, and the concrete repair works required.
Services include
- Surface preparation (high pressure jetting, grit blasting and mechanical preparation)
- Concrete breakout by either traditional mechanical break out or hydro-demolition
- Repair and preparation of steel reinforcement
- Corrosion protection of steel reinforcement (Steel primers, Sacrificial anodes, cathodic protection)
- Concrete reinstatement by hand application, wet and dry spray application techniques
- Application of corrosion inhibitors
- Application of protective and surface coatings
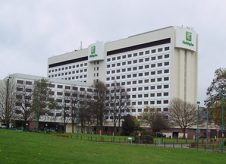
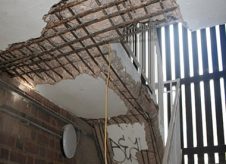
Sectors
- Aviation Industry, Bridges and Tunnels, Buildings, Construction Industry, Education, Food And Drink Industry, Health Care, Heritage And Listed, Highways, Hotel and Leisure, Local Authorities, Marine Structural Refurbishment, Ministry of Defence, Multi-storey Car Park, Nuclear, Petrochemical Industry, Pharmaceutical Industry, Rail, Social Housing, Water Industry
Benefits
Directly Employed Workforce
Highly Skilled and Experienced Operatives
Certified Training
Accreditations
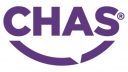
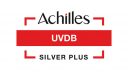
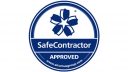
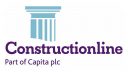
Licensed applicator of all major concrete repair manufacturers
Frequently
Ask Questions
Technical Questions About
Concrete Repair
Frequently asked questions about Total Specialist Maintenance concrete repairs, for problems and technical queries regarding system suitability
For any additional information that is not listed please contact our technical team
Concrete can be repaired, however we may need to understand what is causing the deterioration of the concrete such as carbonation, chloride attack, Fire damaged concrete, Impact damage, heat damaged in order to provide a solution to the problem.
To repair concrete this will involve
- Breaking the out the damaged concrete to approximately 50mm to the underside of first reinforcement layer
- Mechanically prepare the steel reinforcement
- We may have to install sacrificial anodes to the reinforcement
- Applying a cementitious steel reinforcement primer
- Installing a polymer modified concrete repair mortar either by hand or spray application
- We may have to install an impregnation corrosion inhibitor
- We may have to install a fairing coat levelling mortar
- We may have to install a anti-carbonation paint system
Cracked concrete can be repaired as along as the host structure is sound, underlaying soils are not causing subsidence, using various repair techniques such as
- Traditional concrete repair methods
- Sprayed concrete repairs (dry and wet spray techniques)
- Structural crack injection
As part of our comprehensive structural investigation service, we offer the Ferroscan FS 10, a portable detection, measuring and mapping system which provides an immediate liquid crystal image of the reinforcement within the survey area.
Reinforcement analysis may be undertaken using two main modes of operation, Ferroscan Quickscans and Ferroscan Image Scans.
Ferroscan Quickscans
In the Quickscan mode, the data recorded includes the position and cover to reinforcing bars lying at right angles to the direction of the scan. Multiple scans each of up to 10m in length are possible.
Ferroscan Image Scans
Image scans produce a full image of the reinforcement within the scanning areas. The data gathered can be used to supply the following information:-
- Arrangement and position of reinforcement
- Depth of cover
- Indicative bar diameter
The images may be evaluated by viewing transverse or longitudinal sections, ‘slices’ at different depths, and by producing statistical information.
All scanned data can be downloaded onto a personal computer for further analysis, interpretation and printed output.
New concrete is highly alkaline, typically pH 12 – 13, in this alkaline environment a passivating oxide layer develops on the surface of the reinforcing steel, which protects the steel by preventing corrosion.
Atmospheric carbon dioxide reacts with the products of cement hydration converting the Calcium Hydroxide into Calcium Carbonate, a process known as carbonation.
Ca (OH)2 + CO2 CaCO3 + H2O
The conversion from the highly alkaline soluble Calcium Hydroxide into insoluble Calcium Carbonate results in a reduction in the alkalinity of the concrete. This process starts at the surface of the concrete and progresses inwards over a period of time, the extent of the carbonation at a given time being measured from the surface is referred to as the depth of carbonation, the limit of the carbonation being referred to as the carbonation front. When the carbonation front reaches the reinforcing steel the passivating oxide layer is lost and corrosion can commence. The corroded steel occupies a volume up to 12 times that of the original steel, causing the development of expansive forces, which in time cause cracking and spalling of the concrete.
Phenolphthalein solution is used to test the carbonation depth, within the various concrete elements.
Phenolphthalein solution is sprayed immediately into the hole. Where the concrete turns pink in colour, this indicates good Alkali concrete. Where the concrete stays clear, this indicates carbonated concrete. We measure the depth of carbonated concrete from the front face; this is called the carbonation front.
A more complex reinforcing steel corrosion mechanism is chloride-induced attack. There are two ways in which chlorides can enter the concrete, one being externally from road salts or from exposure such as coastal locations.
The other being cast in, in simple terms calcium chloride accelerating admixtures, commonly used in the early 1960s to accelerate building programmes through rapid curing. This type of chloride attack is the most common within concrete structures of this type.
The effect of chloride salts depends to some extent on the method of addition. If the chloride is present at the time of mixing, the calcium aluminate (C3A) phase of the cement will react with the chloride to some extent, chemically binding it as calcium chloroaluminate.
In this form, the chloride is insoluble in the pore fluid and is not available to take part in damaging corrosion reactions. The ability of the cement to complex the chloride is limited, however, this depends on the type of cement.
Sulphate resisting cement, for example, has a low C3A content and is therefore less able to complex the chlorides. In any case, experience suggests that if the chloride exceeds about 0.4% by mass of cement, the risk of corrosion increases.
This does not automatically mean that concretes with chloride levels higher than this are likely to suffer severe reinforcement corrosion: this depends on the permeability of the concrete and on the depth of carbonation in relation to the cover provided to the steel reinforcement.
When the concrete carbonates, by reaction with atmospheric carbon dioxide, the bound chlorides are released. In effect this provides a higher concentration of soluble chloride immediately in front of the carbonation zone. Normal diffusion processes then cause the chloride to migrate into the concrete. This process, and normal transport of chlorides caused by water soaking into the concrete surface, is responsible for the effect sometimes observed where the chloride level is low at the surface, but increases to a peak a short distance into the concrete (usually just in front of the carbonation zone).
The increase in unbound chloride means that more is available to take part in corrosion reactions, so the combined effects of carbonation and chloride are worse than either effect alone.
The categories of risk associated with chloride induced attack are as follows:
Negligible, Low, Moderate, High, Very High, and Extremely High.
Categorisation varies with source of Chloride, age of the structure and extent of carbonation.
The half-cell potential test is the only corrosion monitoring technique
standardized in ASTM C876 – 15: Standard Test Method for Corrosion Potentials of Uncoated Reinforcing Steel in Concrete. It is used to determine the probability of corrosion within the rebar in reinforced concrete structures.
Half-cell potential refers to the potential developed at the electrode of each half cell in an electrochemical cell. In an electrochemical cell, the overall potential is the total potential calculated from the potentials of two half cells… Potential vulnerability of element surface area to corrosion.
Galvanic corrosion requires different metallic elements in contact with each other together rain or saline water providing a corrosive effect.
If all elements are present at the same time, the corrosion process starts which means that the more prominent element will become a cathode and the rate of corrosion will corrode more slowly
Alternatively, the most active element will become an anode and will enhance the rate of corrosion. The increased corrosion rate of the anode is called Galvanic Corrosion.